Mordanting wool and cellulose fibers
Mordanting is an essential process of natural dyeing that was discovered and widely used since ancient times. Mordants help fibers bond chemically with dyes, improving the wash fastness and lightfastness of natural dyes.
SUPPLIES
As always, I used the same natural dyeing supplies that we offer in our shop. Below is a link for ingredients and fibers that you can use to mordant your textile:
RELATED ARTICLES
If you are new to natural dyeing, I would recommend starting with these articles that cover the basics of scouring, equipment, and safety.
Safety and equipment
A QUICK GLIMPSE INTO
MORDANTING HISTORY
The original meaning of mordant comes from the Latin word mordere, meaning "to bite or sting." It is said that in the past it was thought that a mordant helped the dye “to bite” onto the fiber so that it would hold fast during washing.
Most natural dyes require the use of a mordant to achieve the most durable, bright and long-lasting colors. Mordanting prepares the fibers to bond with natural dyes and is typically a separate immersion bath for the fibers. Many materials have been used in the past for mordanting but now the most popular mordant is aluminum potassium sulfate, often called alum. In addition, copper sulfate and iron sulfate have been used since the early days.
Potassium aluminum sulfate. Formula: KAl(SO4)2·12H2O. Also known as alum, potassium aluminum sulfate dodecahydrate, potassium alum, potash alum.
Iron sulfate. Formula FeSO4·7H2O. Also known as ferrous sulfate; iron (II) sulfate, ferrous (II) sulfate heptahydrate, green copperas, green vitriol.
Copper sulfate. Formula: CuSO4.5H2O. Also known as blue vitriol, bluestone, vitriol of copper, roman vitriol.
Nowadays the most common mordant is alum, which was used since ancient times. The historic alum mines were located in France, Italy, Greece, Egypt, Turkey, and many other places. Dating back over 4000 years, evidence of alum's use in textile dyeing spans the globe. Beyond its historical significance, alum was a prized commodity in trade, renowned for its prowess in producing deep, vibrant hues.
In the Mediterranean since the 3rd century, other metallic salts like iron sulfate and copper sulfate have played dual roles as both mordants and color modifiers. While alum suffices for basic mordanting, seasoned dyers can embark on more adventurous paths, experimenting with acids, cream of tartar, iron, copper, natural tannins, and an array of other intriguing materials.
WEIGHT OF FIBERS
Before delving into the recipes, it's essential to understand the commonly used term - WOF. WOF is an international abbreviation, representing 'Weight of Fiber,' expressed as a percentage. It provides information on the amount of dye or mordant needed for a specific weight of dry fibers. For instance, 12% WOF alum indicates using 12 grams of alum for 100 grams of dry fiber. Another example would be 150% WOF of alder bark, signifying the use of 150 grams of alder bark for 100 grams of dry fiber.
Example of calculating 12%WOF for different quantities of fibers:
0.12 × 100 grams = 12 grams
0.12 × 200grams = 24 grams
0.12 × 370grams = 44.4 grams
RECIPES FOR MORDANTING WOOL
MORDANTING WOOL WITH ALUM
Ingredients:
Clean scoured wool
12% WOF alum
4-6 liters of water for each 100 g of wool
Optional:
5-6% WOF cream of tartar (if you are using water that has lots of iron in it)
A pinch of water softener also known as calgon C, hexasodium salt or sodium hexametaphosphate (if you are using hard water)
Mordanting process:
Dissolve alum in a small amount of hot water
Add alum to the pot filled with room temperature water. Stir well.
If using, then dissolve cream of tartar or water softener in small amount of water.
Add solutions to the main pot with alum. Stir well.
Add scoured wool which has been soaked in water for at least 30-60 minutes.
Slowly heat to 75-85°C. Maintain this temperature for about 1 hour. Do not agitate the wool when the temperature exceeds 35-40°C.
Turn off the heat and let it cool to room temperature.
Remove the wool and gently squeeze.
Rinse carefully in room temperature water to remove excess alum and proceed to natural dyeing.
You can dry the mordanted wool and store it for later use. For storage, remember to label it as “mordanted”.
Additional notes and tips:
Wool can be felt when agitated in hot temperatures, so it's best to stop stirring once the temperature reaches 35-40°C. If the wool floats above the water surface or if any other issues arise at higher temperatures, you can gently push it down. However, try to avoid excessive agitation to prevent felting.
Wool can felt or become harsh with sudden changes in temperature, especially when transitioning from hot to cold. It's best to avoid such situations and use water of a consistent temperature when washing wool.
After mordanting you may leave the wool in an alum solution for 1-3 days to increase the mordanting strength.
Instead of leaving the wool to soak in the alum solution you may gently squeeze the wool and transfer it to the bucket with a lid or simply into a plastic bag. Keep closed for 1-3 days to increase the mordanting strength.
If you planning to mordant wool and store it for later use then you may simply hand it to dry without rinsing to save water and time. You will be soaking mordanted wool in water before dyeing it and this soaking will remove excess alum.
If you can’t use a hot mordanting process then you may use a cold mordanting process. Simply add everything to a bucket and leave for 4-5 days. Stir from time to time.
Reuse alum solution. After mordanting, around half of the dissolved alum stays in the water so you may reuse the same solution by adding only half the required amount of alum. For example, if you mordanted 1000 g wool at 12%WOF alum and added 120 grams of alum then after mordanting there should be around 60 grams of alum in the solution. If you are planning to mordant another 1000 g wool in the same liquid then it will be enough to add only 60 grams of alum, because another 60 g are already there.
Even by following the recipe precisely there can still be varying levels of mordant from each batch. Due to this reason, if you need lots of wool for one project to be identical shade, I recommend to mordant all the required amount of wool at the same time to ensure that the final color take-up will be identical.
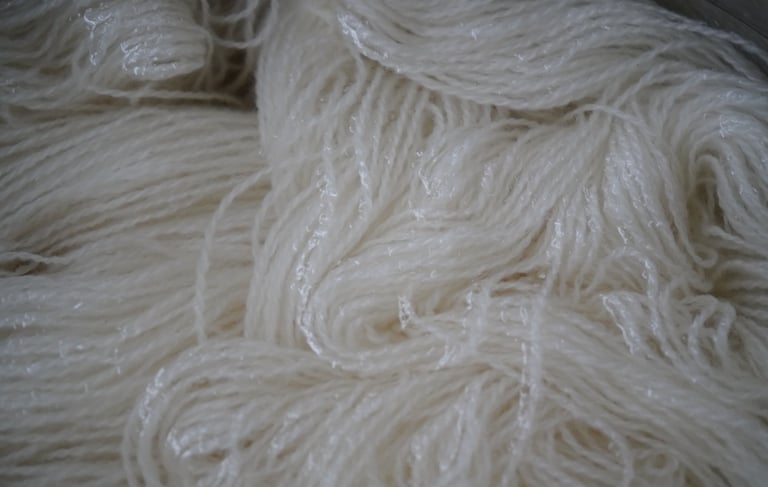
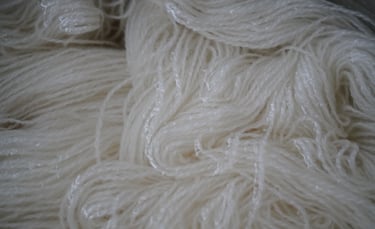
Process of mordanting wool with alum - equipment and wool yarns in the pot.
MORDANTING WOOL WITH IRON SULFATE
Ingredients:
Clean scoured wool
3% WOF iron sulfate (ferrous sulfate)
6-7 liters of water for each 100 g of wool
2-3 tablespoons white vinegar for each 100 g of wool
Mordanting process:
Dissolve iron in a small amount of hot water.
Add iron solution to the pot filled with room temperature water. Stir well.
Add vinegar to the main pot with iron. Stir well.
Add scoured wool which has been soaked in water for at least 30-60 minutes.
Slowly heat to 35-40°C and stir carefully for the first 20 minutes. Ensure the wool does not float above the water surface to prevent uneven mordanting due to iron oxidation.
Then slowly raise temperature to 50-60°C. Maintain this temperature for about 30-50 minutes. Stir occasionally, ensuring the wool does not float above the surface.
Turn off the heat and let it cool to room temperature.
Carefully rinse, changing water until it is clean and clear.
Proceed to natural dyeing or dry and keep for later use. For storage, remember to label it as “mordanted”.
Additional notes and tips:
Be cautious when measuring and using iron; excessive amounts or improper use can make wool harsh and rough. Take extra care during ingredient measurement, stirring, and washing.
Thoroughly wash iron-mordanted fibers before introducing them to a natural dye solution. Even a small amount of iron can lead to unintended color changes, such as shifting red to purple or yellow to moss green. Additionally, it may alter pastels or soft browns from various tree barks or nuts into grey shades.
While mordanting with iron sulfate may initially seem risky or time-consuming, I often achieve wonderful plant-dyed colors when using wool mordanted with iron. In my experience, this method produces deeper, darker, and richer colors compared to iron post-mordanting shades.
Reuse iron mordant solution. You may use this solution to modify naturally dyed colors or add a little amount or iron and mordant the next batch of wool.
Iron sulfate is used by gardeners for various purposes so if you have a garden you may research how to dispose of used iron sulfate solution on plants that would benefit from it.
Iron sulfate on the left, and copper sulfate on the right. They both were common mordants in the past, but nowadays many dyers prefer to use only alum as a mordant
MORDANTING WOOL WITH COPPER SULFATE
Ingredients:
Clean scoured wool
4% WOF copper sulfate
2-3% WOF cream of tartar (optional)
5 liters of water for each 100 g of wool
Mordanting process:
Dissolve copper in a small amount of hot water.
Dissolve cream of tartar in a small amount of hot water.
Add both solutions to the pot filled with room temperature water. Stir well.
Add scoured wool which has been soaked in water for at least 30-60 minutes.
Slowly heat to 50-60°C. Maintain this temperature for about 1 hour. Do not agitate the wool when the temperature exceeds 35-40°C.
Turn off the heat and let it cool to room temperature.
Carefully rinse, changing water until it is clean and clear.
Proceed to natural dyeing or dry and keep for later use. For storage, remember to label it as “mordanted”.
Additional notes and tips:
Wool can be felt when agitated in hot temperatures, so it's best to stop stirring once the temperature reaches 35-40°C. If the wool floats above the water surface or if any other issues arise at higher temperatures, you can gently push it down. However, try to avoid excessive agitation to prevent felting.
Wool can felt or become harsh with sudden temperature changes, especially when transitioning from hot to cold. It's best to avoid such situations and use water of a consistent temperature when washing wool.
If you can’t use a hot mordanting process then you may use a cold mordanting process. Simply add everything to a bucket and leave for 2-3 days. Stir from time to time.
Copper was widely used in the past due to its ability to modify existing natural dye colors and add a great lightfastness and washfastness. But today, there are varying opinions about safey, as it can be toxic in higher concentrations.
I strongly recommend being cautious when measuring and using copper sulfate - wear gloves and a face mask, do not ingest fumes. It would be best to use it outside or in a well-ventilated area dedicated for crafts.
Reuse copper mordant solution. You may use this solution to modify naturally dyed colors or add a little amount of copper and mordant the next batch of wool.
Copper sulfate is used by gardeners for various purposes so if you have a garden, you may research how to dispose used copper sulfate solution on plants that would benefit from it.
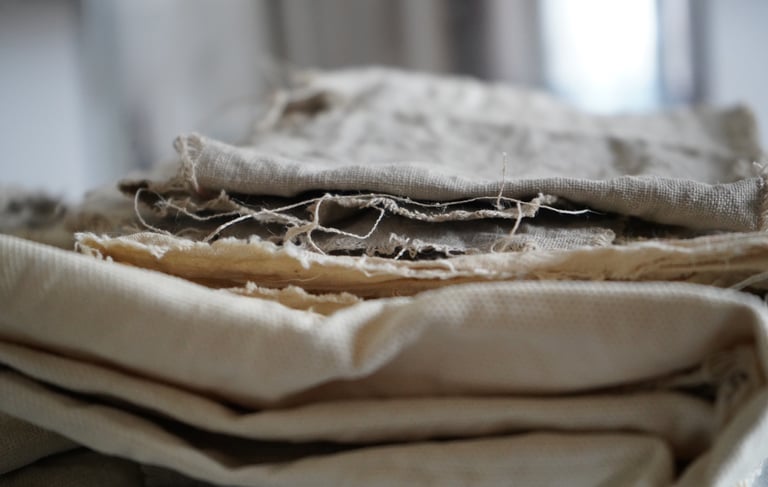

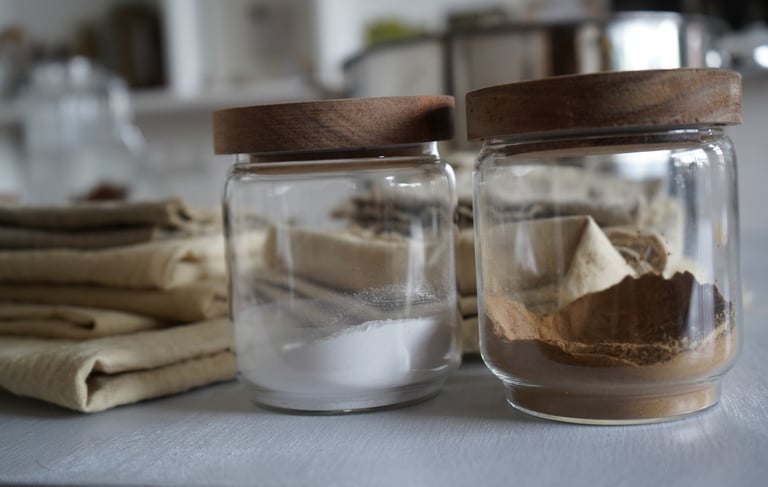
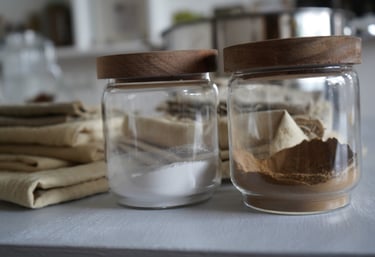
RECIPES FOR MORDANTING CELLULOSE FIBERS
MORDANTING CELLULOSE FIBERS WITH TANNINS AND ALUMINUM ACETATE
This recipe is a 2-step process. Firstly, cellulose is treated with tannins and then mordanted with aluminum acetate.
Ingredients for step 1:
Clean scoured cellulose fibers
10% WOF myrobalan or gallnut extract
3 liters of water for each 100 g of cellulose (30:1 - water:textile ratio)
Step 1. Tannin application process:
Heat water to 40-50°C (usually tap water can reach this temperature)
Dissolve the chosen tannin extract in a small amount of water. Make sure there are no lumps.
Add tannin solution to the water. Stir well.
Add scoured cellulose fibers which have been soaked in water for at least 30-60 minutes.
Keep for 1-2 hours. Stir occasionally.
Take out fibers. Squeeze well, and gently rinse just a little.
Immediately proceed to mordanting.
Additional notes and tips:
In general, you can use any plants with a high concentration of tannins, but I would recommend starting with gallnut or myrobalan extracts.
Using extracts is the easiest way to apply tannins to fabric—you can measure the exact required amount and simply dissolve it in water.
After becoming familiar with the entire cellulose mordanting process, I would advise experimenting with other plants rich in tannins. You can create your solution from various local barks, twigs, or exotic plants. Each plant may not only provide the required tannins but also add an undertone in various shades, brightening your color palette and providing a wonderful experience.
I've come across different recipes for a 2-step cellulose mordanting process in various literature. However, authors Joy Boutrup and Catharine Ellis clearly emphasize the importance of the 30:1 ratio (weight of water to textile) in this process of applying tannins.
Illustrations for tannin application process: dissolving tannin extract in water, soaking cellulose fibers in tannin solution, gently rinsing, and, finally, fibers are ready for aluminum acetate.
Ingredients for step 2:
Cellulose fibers to which tannins have been applied
5% WOF aluminum acetate
5-7 liters of water for each 100 g of cellulose
Step 2. Mordanting with aluminum acetate:
Heat water to 40-50°C (usually tap water can reach this temperature)
Dissolve aluminum acetate in a small amount of water. Make sure there are no lumps.
Add solution to the water. Stir well.
Add cellulose fibers to which tannins have been applied
Keep for 1-2 hours. Stir occasionally.
Take out fibers. Rinse well.
Proceed to natural dyeing or dry and keep for later use. For storage, remember to label it as “mordanted”.
Additional notes and tips:
If you want to enjoy the natural dyeing process and immerse yourself in this wonderful craft using a simpler method, you can choose an easier process to mordant cellulose fibers. Simply follow the recipe for mordanting wool with alum, using only 15-20% WOF alum. While this may result in faster color fading, sometimes it’s not about creating something that lasts forever; instead, it's about enjoying the process and trying out new things.
If you are working with various fibers and have the opportunity, I would advise mordanting only one type of fiber at a time. Different fibers may absorb mordants (and dyes) at different rates, and mordanting multiple fibers simultaneously may lead to uneven results.
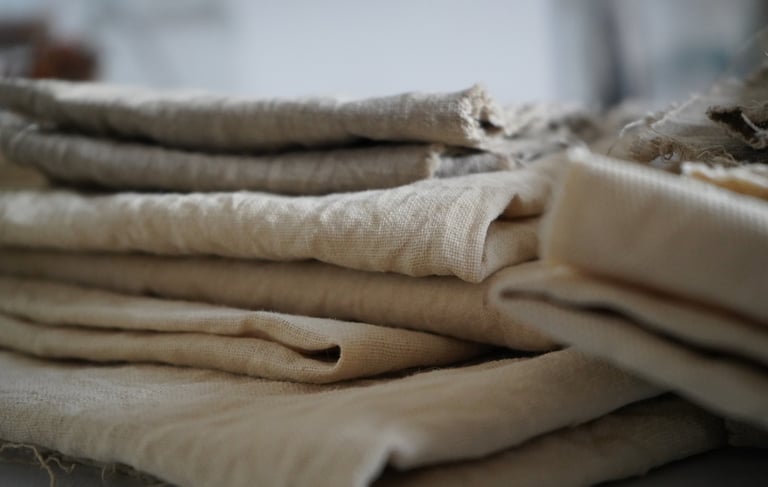
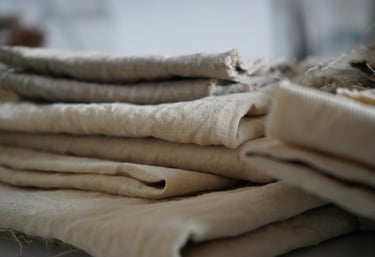
Illustrations for the mordanting process: soaking cellulose fibers in aluminum acetate solution, rinsing in water, and mordant fibers ready for natural dyeing.
© Forests & Meadows 2024
Vilnius, Lithuania
LT-08200
hello@forestsandmeadows.com