Natural dyeing with sappanwood
Sappanwood (lat. Ceasalpinia sappan) produces vivid hues ranging from red, fuchsia, and crimson to purple and burgundy. Its global renown arises from its user-friendly characteristics, making it particularly easy for beginners to achieve vibrant colors. It is impressively efficient - even a small quantity of sappanwood can yield a diverse range of bright tones. In addition, it remains versatile for a long time, creating paler shades like pink, lilac, and mauve. Additionally, this plant holds a fascinating historical background, spanning several centuries, making it worthwhile to explore and remember.
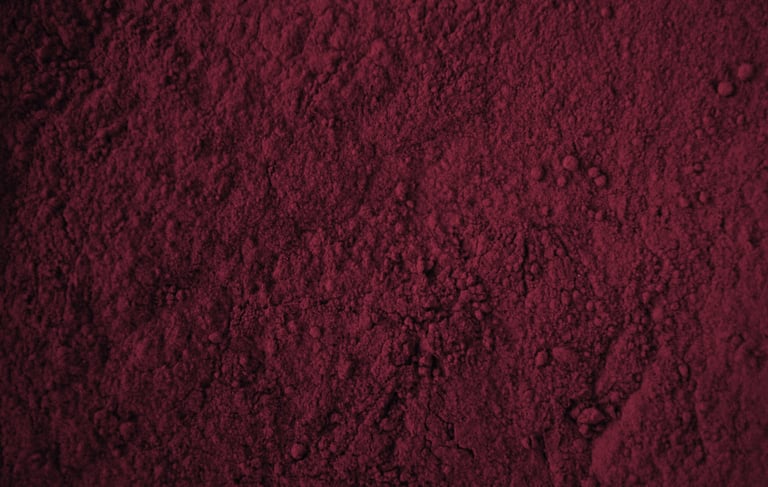
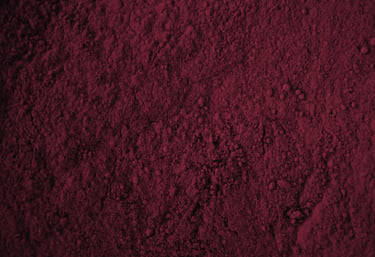
SUPPLIES
As always, I used the same natural dyeing supplies that we offer in our shop. Below is a list of ingredients which you can use to try this recipe:
RELATED ARTICLES
If you are new to natural dyeing, I would recommend starting with these articles that cover the basics of scouring and mordanting.
GENERAL INFORMATION
Name: sappanwood
Latin name: Ceasalpinia sappan
Other names: Other names: Indian brazilwood, Indian redwood, eastern brazilwood, sappan wood, brazilwood tree
Type: mordant dye
Part of the plant used: a core of a tree
Main colorants: brazilin
Main colors: red
Other colors: various shades in a red spectrum such as fuchsia, purple, burgundy, lavender, pink, orange, peach, as well as brown
Purpose: natural dye for textiles, leather, wood, candles, and other natural materials. It can be used for making botanical inks, pastels, watercolors, printing paste, etc.
A GLIMPSE INTO HISTORY
The histories of sappanwood and brazilwood are so intertwined that they should be told together. In fact, these stories are so fascinating in many fields including medieval economics, ecology, colonization, linguistics, medieval dye houses and politics that they deserve their own separate article. I will leave this for the future me to write and now I would like to introduce you with a short version.
The colorant brazilin is derived from the heartwood of various red species of Caesalpinia trees. The Caesalpinia sappan tree, cultivated in Asia, particularly in India, made its way to Europe through the Silk Road. Dye artisans of that era highly prized it for its ability to yield rich and vibrant colors. I believe that the first records about this tree being used in Europe for dyeing were written in the 12th century and it gained more prominence in the 14th - 15th centuries.
During the Age of Discovery, the Portuguese ventured across the Atlantic Ocean and encountered a vast number of these trees, leading them to name the land Brazil. The plant, known as brazilwood, derives its title from the intense fiery red hues it yields. The Portuguese word "brasil," originating from the Spanish "brasa," refers to glowing embers, reflecting the vibrant colors produced by the dye. To this day, Brazil remains the only country in the world named after a dye plant.
The plant discovered in Brazil, Caesalpinia echinata, was soon brought to Europe, where many dyers,fascinated by a cheaper price, began using it in significant quantities, sometimes employing less-than-optimal technological methods. You see, the colors achieved from Caesalpinia trees are not as long lasting as those reds achieved from other significant red dyes such as madder or kermes. Recognizing the risks associated with less persistent dyes, various authorities imposed restrictions. Some regions prohibited the use of brazilwood/sappanwood without blending it with other red dyes, Venice permitted its use only for cotton, and at some point 18th-century England forbade its use altogether.
Despite the wide variety of prohibitions, brazilwood/sappanwood maintained its presence in Europe as it was more affordable for those less fortunate and many more people could enjoy wearing brilliant red colors, at least for a while. The demand for cheaper red dyes increased and forests of Brazil were exploited without proper protection and control. Additionally, it was used for musical instruments and finally it was exploited so much that now this tree is currently a protected endangered species and isn`t used for natural dyeing anymore. The plant, Caesalpinia echinata, carries an important local cultural significance and is referred to as the tree of music, Pernambuco, Santa Martha, Pau Brasil, Paubrasilia and other names.
Usually, the endangered Caesalpinia echinata is called Brazilwood and Caesalpinia sappan is called Sappanwood or Indian brazilwood. Sappanwood is cultivated in Asia and used for natural dyeing purposes.
NATURAL DYEING WITH SAPPANWOOD
The wood for dyeing is supplied in the form of wood chips or fine ground particles. Usual method to create a dye solution is to add boiling water over the mass, leave it overnight and simmer for several hours the next day. It can be strained and used for dyeing as soon as it’s cooled, but it was already back in the Middle ages that dyers noticed that keeping the dye longer for several days or even a month improves the dyeing qualities. The dyed textile is wash-resistant, but eventually gets darker, acquiring a shade of brown in long exposure to light, making it not very suitable for daytime curtains or summer clothes, and it is more suitable for items that don’t get as much exposure to sun. This dye is rather sensitive to various nuances of the water – hardness, softness, minerals, pH and other factors, often determining the final color – bright red, purple, fuchsia or orange.
Ingredients:
Mordanted textile fibers
20-50% WOF sappanwood dye chips or powder
4-6 liters of water for each 100 g of fibers
Dyeing process:
Use 20-50% WOF.
Add hot or boiling water to the dye and leave overnight or longer. After soaking, simmer for 2-3 hours, then let it cool.
Strain using a piece of dense fabric, because the dye particles are very fine and could get tangled in the fiber that you’re dyeing.
You can dry the strained particles and reuse them later a few more times for lighter red or pink shades.
The color of the solution may depend on the water you use – it may be red, purple, or orange. You may add a little chalk to the dye to obtain a brighter red. You can also experiment by adding vinegar (to acidify) or soda ash (to alkalize) the solution. This way you will achieve a wider range of colors.
Add fibers to the dye. Fibers should be soaked in water for at least 30 minutes before adding to the dye solution. Use pre-mordanted fibers.
Heat to 70 - 80°C. The dyeing time depends on the brightness and depth of the color you want to obtain. Dyeing time can vary from 1 to 2 hours or even longer.
After heating, let the fibers cool down in a dye pot. You can leave it overnight.
The dyed fiber can be modified with copper or iron mordants to obtain a wider spectrum of colors. For modification prepare a 2% copper sulfate or iron sulfate solution. Add fibers to the modification solution, keep for 5-30 minutes, and observe the results. Copper will darken the colors and iron will switch it to darker, purple colors. After modifying colors, rinse in water.
After dyeing, hang the fibers to dry. You can leave it for several days. This process is called “air-curing” and it helps fibers to absorb more colorants.
Then wash the fibers carefully. Keep changing water until it is clear. In my experience, sappanwood also reacts with the properties of washing water. So for example, if you modify your dyeing solution with alkaline or acid, then during the washing process colors may slightly change towards the initial colors of the dye liquid.
NATURAL DYEING WITH SAPPANWOOD EXTRACT
Ingredients:
Mordanted textile fibers
4-8% WOF sappanwood extract
4-6 liters of water for each 100 g of fiber
Dyeing process:
A small amount of sappanwood extract can dye a lot - start with using 4-8% WOF and observe the results.
Dissolve the powder in a small amount of warm water and add to your dye pot.
Fibers should be soaked in water for at least 30 minutes before adding to the dye solution. Use pre-mordanted fibers.
Add wet fibers to the dye solution and simmer for 40-60 minutes depending on the shade you want. Leave to cool and soak for a day or two for the deepest colors.
Sappanwood is very sensitive to water and its properties. You may add a pinch of chalk to bring out bright red shades.
To widen your palette even more experiment with additional mordants - iron sulfate or various tannins.
After dyeing, hang fibers to dry. You can leave it for several days. This process is called “air-curing” and it helps fibers to absorb more colorants.
Then wash fibers carefully. Keep changing water until it is clear. In my experience, sappanwood also reacts with properties of washing water. So for example, if you modified your dyeing solution with alkaline or acid, then during the washing process colors may slightly change towards the initial colors of dye liquid.
ADDITIONAL NOTES AND TIPS
Additional Information:
While sappanwood exhibits good resistance to washing, it is more light-sensitive compared to other red natural dyes. Prolonged exposure to sunlight may shift its color towards brown shades, making sappanwood not the best choice for items like curtains or summer dresses.
Tips:
For optimal results, combine sappanwood with madder. Madder provides long-lasting red shades, and sappanwood enhances them, especially when achieving rich reds from madder alone may be challenging for beginners. This combination, rooted in medieval European practices, offers a time-tested recipe for vibrant hues. Remember to prepare each plant separately as they require different recipes. This not only ensures the best outcome but also keeps the overall cost more budget-friendly.
RESULTS
For the purpose of this article, I've taken various fibers and different wools treated with various mordants and dyed them all together in the same solution. I prefer doing this when testing new plants or recipes because it's an excellent way to explore the diverse possibilities one recipe can produce and observe how different fibers or mordants react. I'm particularly excited to share these results with you!
One change I would consider is dividing the solution into two parts, using one for wool and another for cellulose. Through my experiences, I've noticed that wool tends to come out brighter than cellulose. Cellulose, being more challenging to dye, often requires longer simmering and soaking times to develop vibrant colors so I feel that wool fibers take up colorants faster and therefore there's less dye left for cellulose. I've primarily worked with wool, so I hadn't considered separating fibers before, but I'm planning to do this in the future to showcase even better results.
Below are the photos of my results with descriptions of fibers and mordants. Everything was dyed in the same solution of sappanwood extract at 8% WOF, the same way as described in the instructions above. As you can see, 8% WOF gives very dark colors which are even difficult to show in photos, so you may use less if you wish to get lighter shades.
All yarn is the same type of 100% wool, all mordanted with 12% alum. From top to bottom: white wool, light grey wool, greyish brown wool, dark grey wool, greyish brown wool. So there is a wonderful possibility to achieve various wonderful colors simply by using different naturally colored wool.
All yarn is the same type of 100% white wool. From top to bottom: mordanted with 12% alum, mordanted with 4% copper sulfate + 3% cream of tartar, mordanted with 3% iron sulfate. All skeins were mordanted before dyeing. As you may see, even a small amount of copper or iron has a very significant difference when dyeing with sappanwood.
From left to right: the first 6 skeins are the same as in those 2 photos above; white wool mordanted with 10% myrobalan extract, white merino wool mordanted with 12% alum, a blend of grey wool and hemp mordanted with 12% alum. On the far right, there are two linen fabrics.
All yarn in the back row is the same as in the photo above. The fabric in the top row is white linen, the other one is waffle-woven linen in white and natural grey colors, both mordanted together with 10% myrobalan extract and 5% aluminum acetate. The front row from left to right - 100% white cotton, 100% natural boucle linen, mordanted together with fabrics. The remaining skein is 100% white silk mordanted with 15% alum. What is very interesting and weird is that those little pink skeins of cotton and linen are much lighter than those linen fabrics - usually, they obtain similar shades. They were definitely mordanted together so I am wondering if maybe somehow I added them in the dye pot later and haven't written a note about this.
After dyeing the first batch of fibers (at 8% WOF) I added 350 grams of wool mordanted with 12% alum to the same dye bath. The skein on the left was dark grey natural wool, the skein on the right was white wool. They were difficult to photograph so I'm adding another photo below.
Same yarn as above. After dyeing these yarns I added 400 grams of alum-mordanted dark grey wool to the same dye bath for the third time. This time the color was very unimpressive on dark grey wool, but I know that sappan produces light shades for a long time, so I prepared a fourth batch of yarn. This time I added 400 grams of white alum-mordanted wool and I added a pinch of iron sulfate to the dye bath and the yarn obtained a light mauve color.
© Forests & Meadows 2024
Vilnius, Lithuania
LT-08200
hello@forestsandmeadows.com